With the expansion of various industries, the application of nylon cable ties has broadened significantly, encompassing nearly every sector. As a result, the number of manufacturers producing nylon cable ties has increased annually, leading to a wide disparity in technology and quality. Consequently, the market is flooded with products of varying standards. Therefore, understanding how to discern the quality of nylon cable ties is essential to ensure you get the best value and performance for your needs.
Quality can be assessed from two key aspects:
Common flaws in plastic products such as burrs, material shortages, scorching, silver streaks, bubbles, deformation, and shrinkage are also prevalent in nylon cable ties. It’s crucial to examine the appearance closely. Some imperfections might not affect functionality but could pose potential quality risks. Of particular importance is the quality of the teeth and the head cavity of the cable tie, as these are critical components. The teeth should be intact without any missing parts, and the inner surface of the top part of the head cavity should not have any step-like mold deviations. Such defects can lead to a high incidence of unusable ties due to slipping teeth and insertion difficulties, rendering them nearly useless. Paying attention to details, like the size of the burrs, is important because excessive burrs can lead to a loose fit between the tie strap and the head cavity, resulting in slippage. Generally, products in their natural color are considered the best as this is a universally accepted axiom. Good nylon cable ties should be clear and bright; even a slight yellowing is acceptable, but they should not be cloudy or dark. The quality of the material used is also a crucial factor, especially for PA66, used in nylon cable ties. The molecular structure of the plastic changes after multiple high-temperature melt-shear actions, which is particularly evident in PA66, known for its excellent wear resistance and tensile strength.
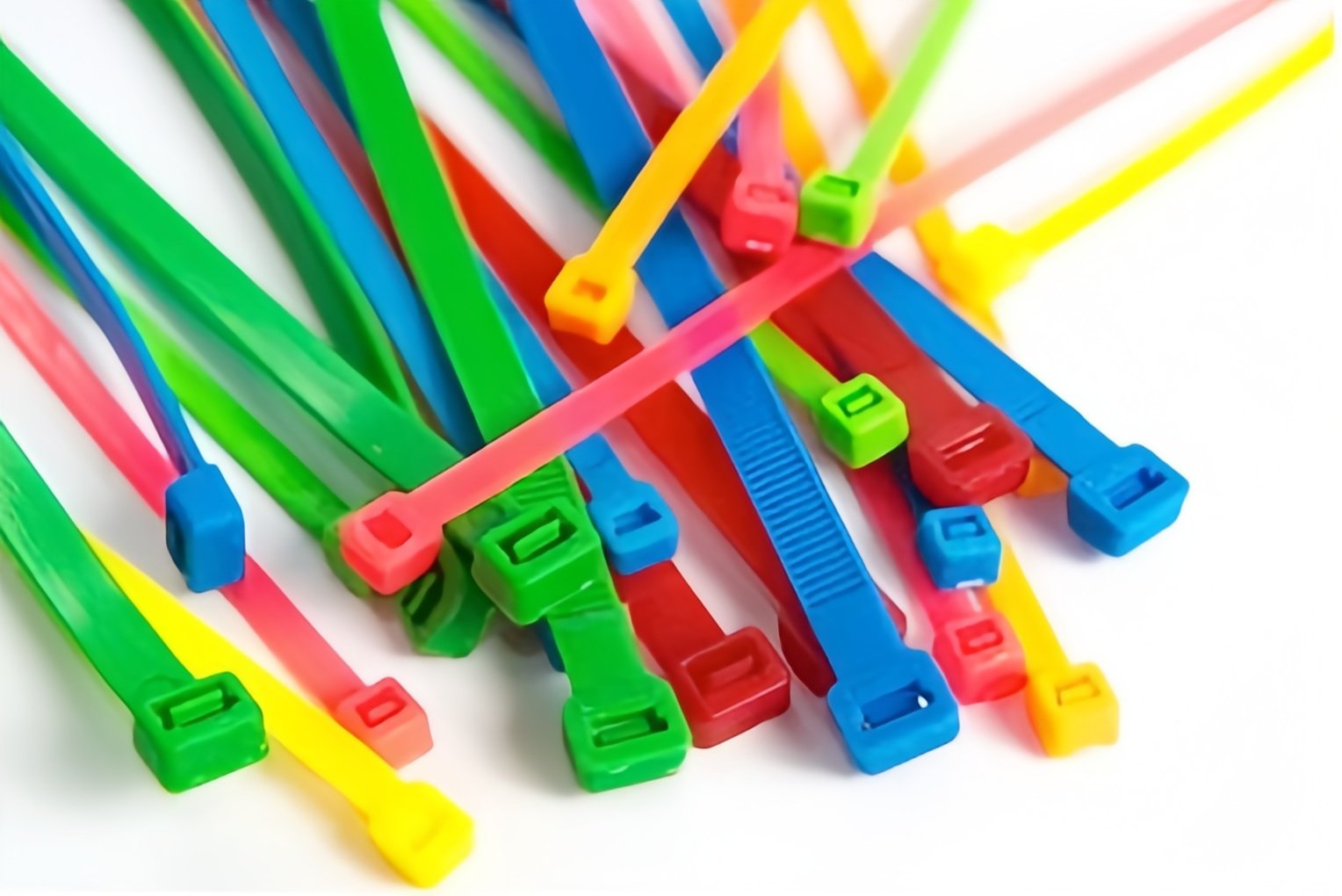
The most critical performance metric for nylon cable ties is their unlocking force. The cable tie should not break, unhook, or have the head crack until the force applied exceeds its nominal tensile strength. Sometimes, perceived poor quality may be due to selecting the wrong specification rather than an inherent flaw in the cable tie, as each specification has a limit to its standard tensile strength. If the required force in an application significantly exceeds this limit, then it’s advisable to opt for a higher tensile strength specification, even though it might be costlier. High-quality cable ties exhibit excellent flexibility and extensibility; they do not break abruptly or become brittle. This adaptability ensures a broader range of applications, potentially reducing costs.
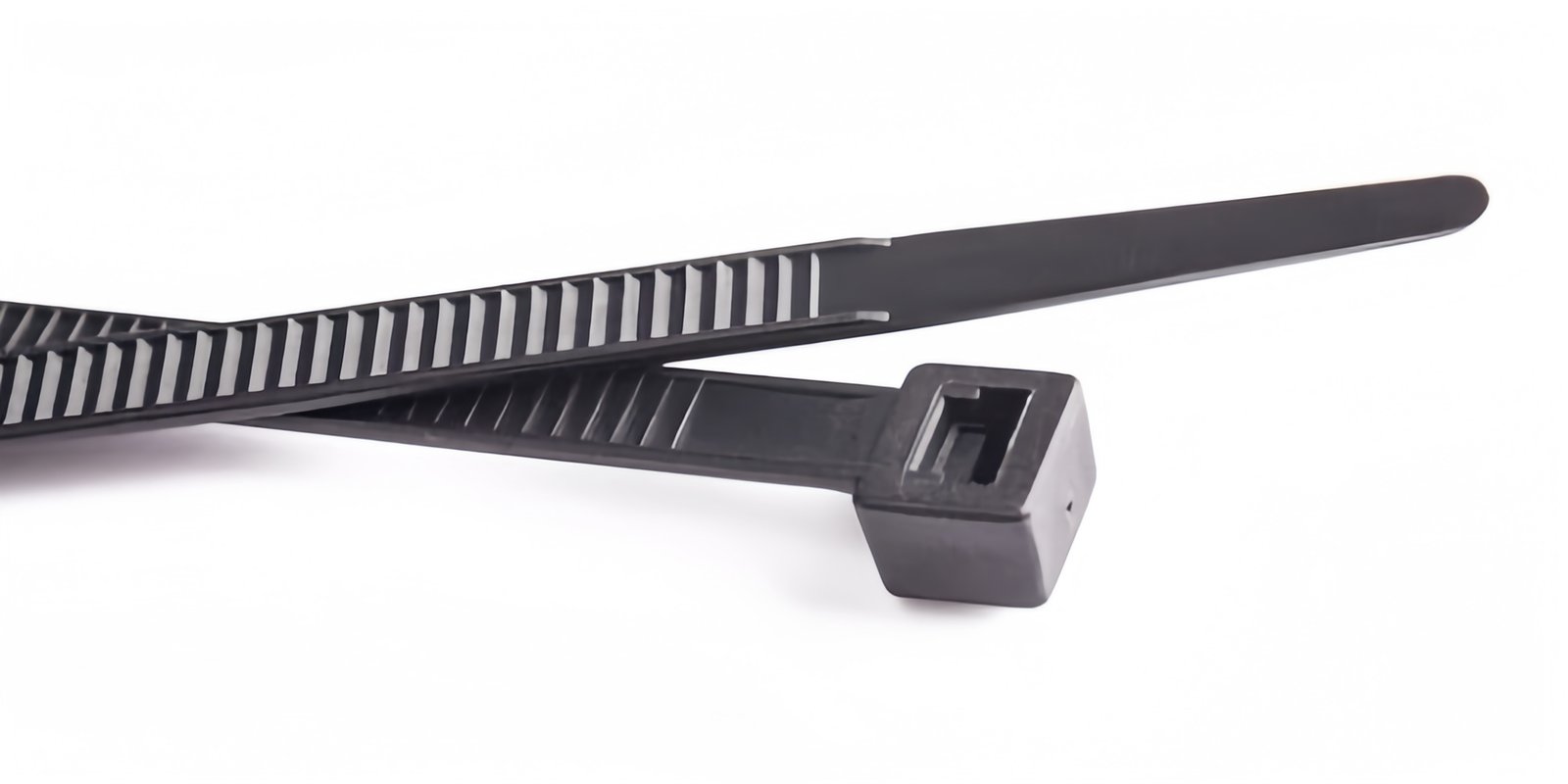
In summary, selecting the right product for your specific needs is crucial. Whether it’s for domestic use or industrial applications, choosing high-quality nylon cable ties can make a significant difference in performance and cost-efficiency.