In the world of cable tie production, selecting the appropriate mold is a critical decision that directly impacts the efficiency, quality, and overall success of your manufacturing process. With a variety of molds available on the market, understanding the nuances and specific benefits of each type is key to making an informed choice. In this guide, we will explore the three main types of cable tie molds: hot runner, standard cold runner, and ordinary cold runner molds.
Each mold type offers distinct advantages and serves different production requirements. From the high-quality output of hot runner molds to the cost-effectiveness of ordinary cold runner molds, your choice should align with your quality standards, production experience, and machinery capabilities.
Ideal for those demanding the highest quality, the hot runner mold produces cable ties with superior tension and durability. Its user-friendly operation makes it a favorable option for beginners. However, to harness its full potential, it is advisable to use injection molding machines with a capacity of over 400 tons.
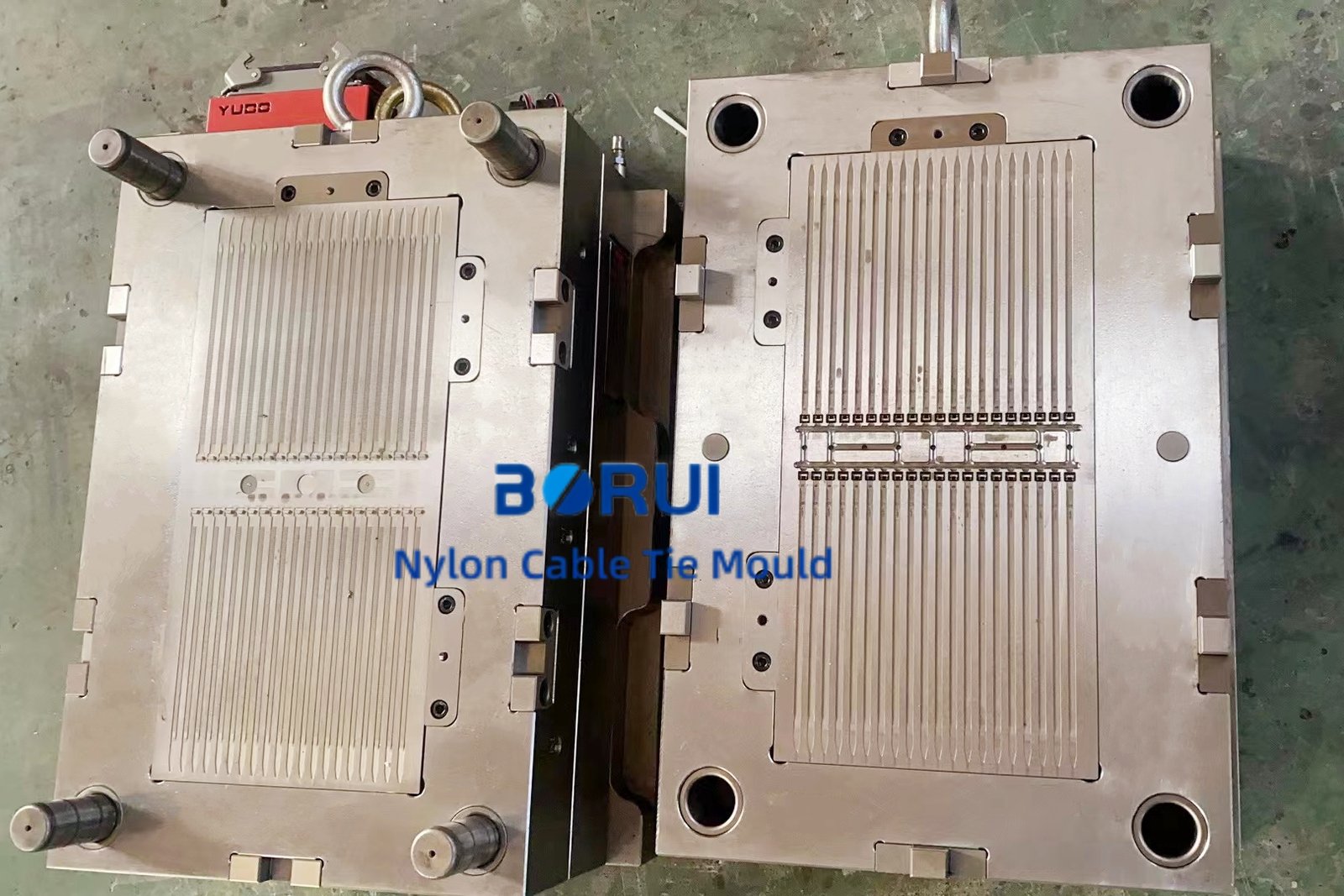
A popular choice among mid-sized businesses, this mold type balances quality with affordability. With a lifespan of up to 3 million cycles, it’s a robust option for consistent production.
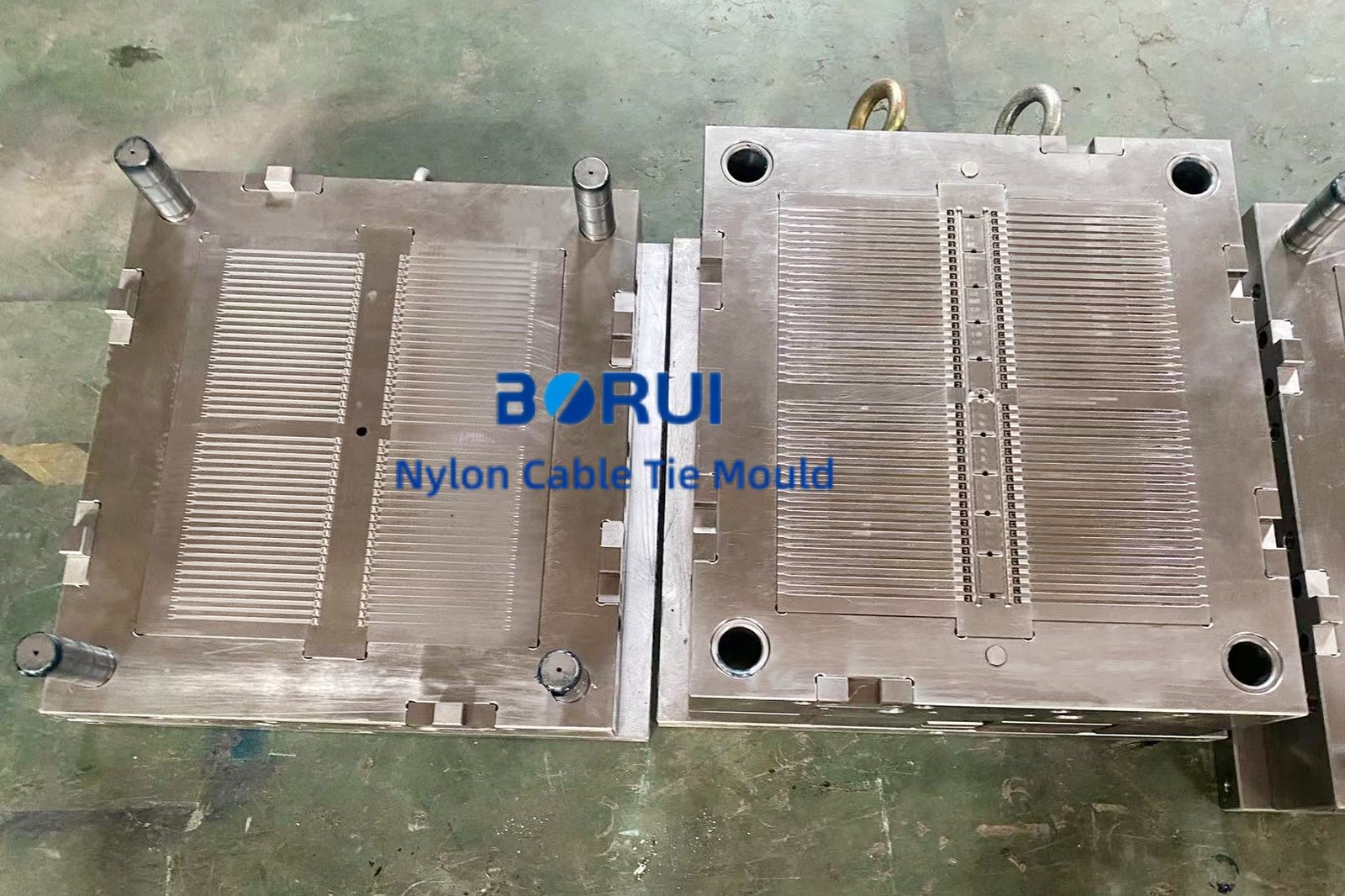
While it delivers a quality comparable to the standard cold runner mold, the ordinary mold differs in structure and material, offering a lifespan of about 1 million cycles. This can be an economical alternative for smaller scale operations or those with budget constraints.
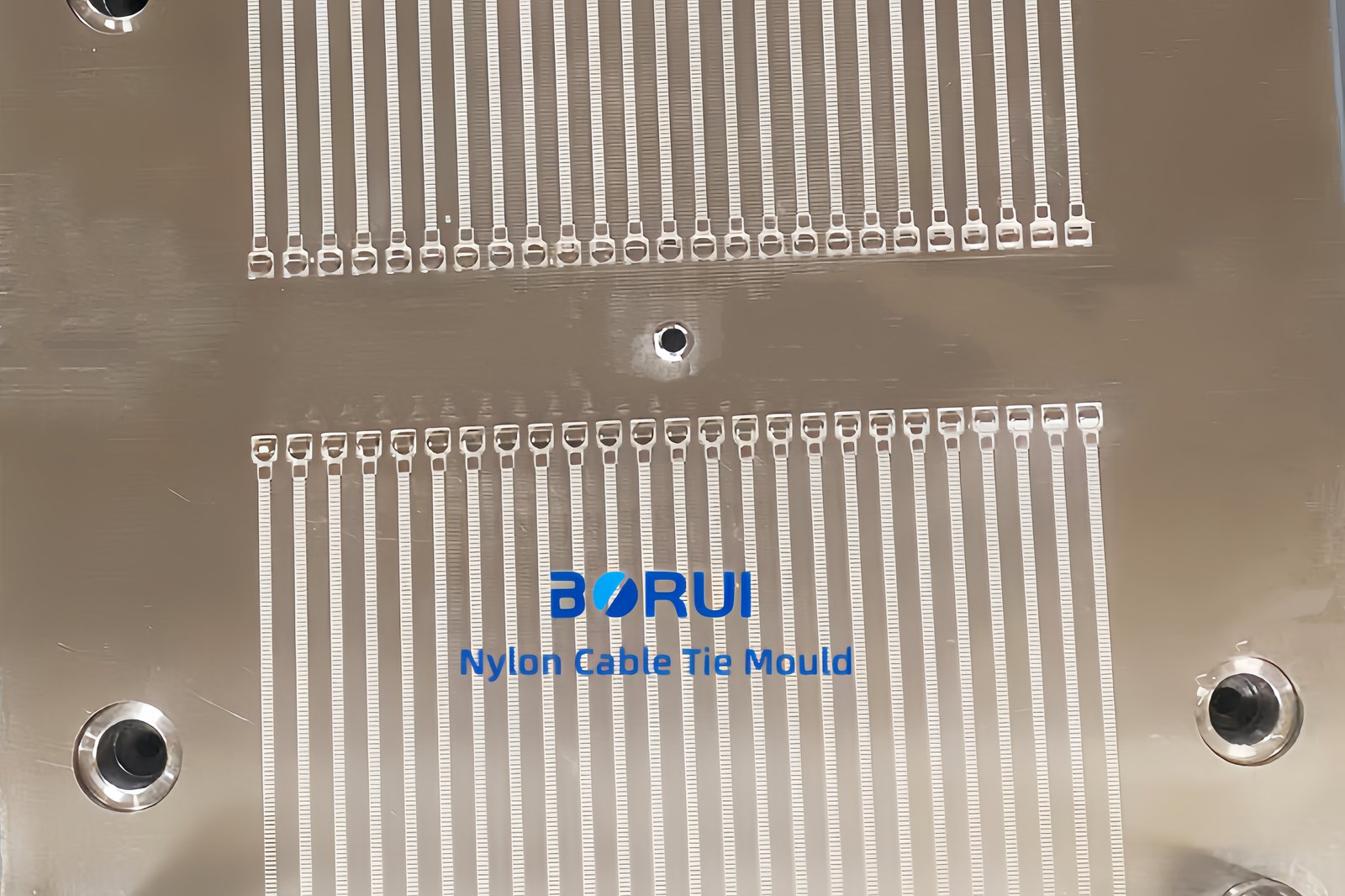
For those eager to delve deeper into the cable tie manufacturing world, I am here to assist. From advising on the suitable injection molding machine and nylon material to choosing the right mold and understanding cable tie dimensions, I aim to be your go-to resource. Let’s navigate the complexities of cable tie production together and tailor a solution that best fits your unique manufacturing goals.